A DIY Guide – The Secret’s Behind the Perfect Hole Saw Technique. Plaster hole saw
A DIY Guide – The Secret’s Behind the Perfect Hole Saw Technique
A workman’s staple, the hole saw is a tool you’ll encounter as you start to flex your DIY muscles and branch out into more interesting challenges. They’re used to cut perfectly round holes in a variety of materials. Wood and plaster are common workpieces, but metal, glass, ceramic, concrete, and stone still fall to the hole saw.
Despite the name, this tool looks more akin to a drill bit than a saw – in fact, its cutting edge rests at the end of a large diameter cylinder, and this is spun on a power drill to cut through your chosen material.
Where might you use a hole saw? Here are just a few ideas:
- Installing hardware (such as dead bolts or locks) on doors
- Cutting holes in ceilings to accommodate light fixtures or fittings
- Cutting holes to accommodate drainage or waste pipes
- Making extra connections in pre-existing pipework
- Cutting vents in masonry
- Cutting holes for cables and wires
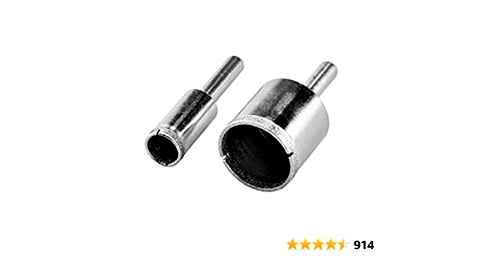
That list is far from comprehensive, but it illustrates the tool’s diverse array of applications. Learning to use a hole saw is undeniably useful, so let’s get into:
- What a hole saw is
- Why you should use one
- The types available and how to choose the right one
- How to attach hole saw to drill
- How to operate your hole saw
- How to care for your hole saw
- How to keep yourself safe
All in all, you’ll find yourself fluent in hole saw by the time you finish reading this post.
What is a Hole Saw?
Also known as a hole cutter, and sometimes spelled ‘holesaw’, the hole saw is easy to understand but deceptively tricky to master. Let’s start by covering what it is, how it works, why you’d use one, and what components it’s made from.
The hole saw is a large diameter, hollow drill bit with a keen cutting blade along the outer edge. Attach one to a power drill and it rotates at high speed, cutting precise holes into anything from bathroom basins to external walls. The depth of cut is limited by the hole saw’s cup-like shape, but a variety of bit types are available to work around varying requirements.
Metal Cylinder
The body of a hole saw is a wide diameter metal cylinder. Regardless of your cutting edge, steel is standard across the lion’s share of industries. The cylinder is mounted on an arbour, and you’ll notice slots cut into its walls to facilitate the ejection of chips and dust for smooth performance and to prevent stuck blades. Slot number varies between makes and models – 6 is generally the upper limit since more would compromise the hole saw’s strength, and we wouldn’t want that.
Here’s where things get interesting. The metal cylinder of each hole saw culminates with an edge that uses either serrated saw teeth, gulleted/square teeth, or ultra-hard embedded materials to cut through your workpiece.
- Serrated Saw Teeth: Typically set at a 60° angle to allow a penetrating bite into the material being cut, saw teeth are far and away the most common cutting edge. Use saw tooth hole saws for wood, plaster, softer metals, and plastic.
- Gulleted/Square Teeth: Teeth are wider set since raw power is preferred over fine cuts. You’ll use gulleted or square tooth hole saws with more abrasive surfaces, including concrete, brickwork, ceramic tiles, glass, and stone.
- Coated: No teeth are used at all. Instead an ultra-hard material, usually tungsten carbide or diamond, coats the cutting edge. of a niche tool, you’ll use coated hole saws to cut through heavy-duty metals, ceramics, and concrete. Unless you’re a professional, you’re unlikely to encounter the need.
You’ll also want to pay attention to the pitch of teeth and their TPI (Teeth Per Inch) rating, so let’s break down the impact of each factor.
Pitch
Pitch refers to the distance between the point of two teeth (serrated) or the middle of two teeth’s gullets (gulleted/square). A variable pitch hole saw varies that distance, while a constant pitch hole saw maintains the same distance.
- A variable pitch breaks the sawing rhythm; that might sound like a bad thing, but it inhibits vibration for a smoother cut, reduced blade wear, and lower noise levels. Chips and dust eject easily to reduce the chance of clogging or overheating.
- A constant pitch works slower but produces a much finer cut.
TPI
Understand TPI as a measure of tooth frequency along the blade. For example, 18 TPI means 18 teeth per inch, so that tooth frequency is higher than that of a 16 TPI hole saw. TPI numbers vary, but they stay within the general ballpark of 20 to 2.
- Blades with a higher TPI will cut slowly, but, less likely to tear at the fibres of your material, they also cut smoothly.
- Blades with a lower TPI cut faster, but they do tend to tear at fibres to produce a more ragged edge.
Arbor
The arbor isn’t specific to the hole saw, but it’s a vital part nonetheless. It’s the type of tool bit used to grip other moving tool components, essentially the connecting part between your hole saw and your power drill. Most, but not all, hole saws are supplied with an arbor – you’ll occasionally need to purchase your own, so pay attention when you buy.
As you’re browsing, you might consider seeking an arbor with a spring placed over the drill bit. These are known as ejector springs – they contract as you drill and then eject the slug (the cut segment) after the hole has been made.
Arbors can be broken down into fixed or detachable and small or large.
- Fixed Arbors: Said to have an ‘integral shank’, fixed arbors come attached to the hole saw blade. Using one means skipping any dismantling when you need to change saw size.
- Detachable Arbors: Unfixed to the hole saw, detachable arbors can be used with a variety of blades. Using one means skipping the need to purchase again for every hole.
Size comes down to the diameter across the flats of an arbor’s hexagonal shank – so, the distance between one flat face to the opposite flat face.
How To Cut PERFECTLY CIRCULAR HOLES! (Hole Saw Bit/Circle BitCut Circles in Wood, Drywall, PVC!)
- Small Arbors: Have a shank size of 1/3-inch (8.75mm) and are used alongside hole saws with diameters between 14mm – 30mm (1/2 – 1 inch).
- Large Arbors: Have a shank size of 7/16 inch (11.1mm) and are used alongside hole saws with diameters between 32mm – 210mm (1 – 8 inches).
Hole saw sets often provide an arbor adaptor. This straightforward threaded attachment fits over your drill bit and onto the collar threads of a large arbor, allowing users to attach a smaller hole saw to the adaptor’s threads.
Drill Bit
You’ll find a drill bit at the centre of each hole saw. Their function is to create a pilot hole, anchoring the hole saw in place to decrease any ‘wandering’ as the cut is made. At the other end of the drill bit is a blunt hexagonal shank that is inserted into and gripped by your power drill’s chuck.
Why Use a Hole Saw?
Let’s take a breath before diving into the particulars of using a hole saw to consider why exactly you’d want to. Other tools can cut holes, so what makes a hole saw the go-to among professionals?
- Leaves the Core Intact: A hole saw works without needing to cut up the core of your workpiece, a notable advantage over twist drills or spade drills, especially when dealing with larger holes.
- Reduced Friction: The walls of the hole saw cylinder are relatively thin, cutting through material with less friction than solid drill bits. Less power is needed, so less strain is placed on your drill and cutting time is drastically reduced. Expect to save on energy, battery life, and time.
- Versatility: A hole saw achieves a greater variation of hole sizes than rival tools – they are particularly valued for cutting large diameter holes.
Types of Hole Saws
We’ve covered how the individual components of a hole saw can differ, but more important is the variation between hole saw types. There are plenty from which to choose, and your decision should be based around:
Keep those points in mind as you peruse our quick overview of common hole saw types:
- Carbon Steel: Your basic general-purpose hole saw performs admirably for the DIY expert or enterprising home-improver. Though not the most durable, carbon steel hole saws are ideal for use with softer materials, including wood, non-laminated plastic, and plasterboard.
- Variable Pitch Bi-Metallic: Bi-metal construction boosts safety by eliminating the chance of shattering, so consider these a good step-up for dealing with slightly tougher materials or working for longer periods. Many boast hardened teeth of high speed steel for faster cutting, and variability lets you cut at different speeds according to your chosen material. Best suited to hardwood, plywood, non-laminated plastic, plasterboard, and non-ferrous metals (such as aluminium, zinc, and copper).
- Deep Cut Variable Pitch Bi-Metallic: Not named through coincidence, the deep cut variable pitch bi-metallic hole saw drill will boast a cut depth up to 42.5mm. Otherwise, it retains the characteristics and benefits of the standard bi-metallic.
- Constant Pitch Smooth Cut: The constant pitch smooth cut hole saw utilizes high speed steel with a tough alloy body. Hardened, abrasion-resistant, and heat-resistant, they’re made for cutting stainless, tool, and mild steel. Plasterboard, wood, and thin plastics also work well. Something to note, the hexagonal shank will sport a slight indentation. Nothing to worry about – it just helps lock the shank into place.
- Tungsten Carbide Tipped: Tungsten carbide tipped teeth deliver fast cutting action and outstanding durability, ideal for those who expect to use their hole saw frequently and for extended periods. Often used as the construction industry’s multi-purpose option, they cut through all woods, plastics, tiles, and metals. Perhaps not quite necessary for personal use, but undeniably nice to have.
- Welded Shank Soffit Cutter: A non-detachable arbor is welded to the base plate, and the saw is made from high speed steel with a variable tooth pitch. A wide diameter makes them seem tailormade for cutting vent holes in soffit boards, and they work well with plywood, metal, and PVC.
- Diamond-Edged: Showcasing a conspicuous absence of teeth, such hole saws are either coated or infused with diamonds. The hardness and durability is exceptional, so high heat and constant resistance are no obstacle. You’ll generally use them to drill through ceramic tiles. Though heat resistant, you should periodically cool them in water.
- Multi Hole Saw: Designed to be used for cutting a range of different diameter holes, the multi-hole is notoriously undiscerning when it comes to material. Wood, non-laminated plastics, plasterboard, chipboard, plywood, and non-ferrous metal (except stainless steel) can all be cut through.
Finally, two separate configurations allow for on-the-fly adjustability:
- Adjustable: Adjustable hole saws allow multiple sizes of holes to be made with the same machine. Portability is improved since everything is contained within a single unit, and you’ll be able to work with various materials without changing up.
- Circle Cutter: One, two, or three adjustable teeth sit on a platform with the pilot bit. Adjusting them allows users to cut holes of almost any size, even beyond a foot in diameter. Superbly flexible, but they’re quite tricky to use.
How to attach a hole saw to a drill
Hole saws pose potential danger, so knowing when and how to use them is key. Whether you’re cutting through wood or dealing with ceramic, you’ll start by properly attaching the hole saw to the drill.
- Determine Necessary Size: Firstly, check your requirements and set the appropriate size hole saw. Cutting through metal? Make sure there’s a bottle of cutting oil or lubricant close at hand before starting.
- Select Your Arbor: If using a detachable arbor, determine the correct one for your hole saw to fit into. At the same time, ensure you have an arbor that will fit your power drill’s chuck.
- Fit Arbor: Now your arbor is selected, insert it through the back of the hole saw.
- Screw Hole Saw and ArborTogether: Screw the hole saw onto the arbor thread, not stopping until it feels as tight as possible. If adjustable, the arbor should protrude past the teeth by around 3/8 inch and then tighten using the set screw.
- Tighten the Hole Saw: Insert the end of your arbor into the drill chuck. 18 volts is the minimum requirement – anything less won’t produce the necessary torque for proper cutting.
- Tighten Chuck: Screw the arbor in firmly until it is securely held by the chuck.
How to Use a Hole Saw Perfectly
Hole saws seem misleadingly easy to use. It’s no mere matter of choosing a spot before pressing down with your drill, and practice must make perfect until you’re confident. During your first few attempts, try using a practice workpiece.
- Drill Your Pilot Hole: Used to guide the saw, this goes right at the centre of the hole you wish to cut. As you drill, keep the bit level. If your workpiece is freestanding, take the time to secure it to prevent any spinning or other movement.
- Align Drill Bit: Pilot hole made, it’s time to align your arbor’s drill bit within. Check the hole saw’s teeth are all in even contact with the workpiece. If cutting metal, drip a little cutting oil or other lubricant over the blade before starting.
- Keep it Steady: You’ll want to start slow, holding the grill tightly and squeezing the trigger lightly. Only a moderate amount of pressure is needed to push the saw through – instead of forcing it, FOCUS on keeping the saw level.
- Eject Dust and Chippings: Take regular pauses so you can back the drill out from the hole and clear it of dust and chippings. Doing so helps avoid clogging and overheating.
- Saw from the Other Side: To make the final hole smoother, finish your cut from the opposite side, if possible.
- Remove Slug: The slug is just an easy term for the waste material that collects in your hole saw. If you have an ejector spring arbor, it should pop right out – otherwise, dig it out manually.
That covers the basics, but what if you need to drill holes deeper than your hole saw allows or widen an existing hole?
Here’s how to cope with both situations, starting with deep drilling.
- Cut to Depth: As detailed above, use your hole saw to achieve the maximum depth possible.
- Use YourChisel: Grab a chisel and start cutting out as much wood as you can. This should let you go a little deeper.
- Continue Cutting: Once the wood has been cleared, realign your saw and continue until you reach the required depth or make a through-hole.
- Use an Arbor Extension: For added depth, consider buying and attaching an arbor extension. These are long metal rods with a socket on the end to accept the shank from your arbor, and you can use one to reach deeper into holes than conventionally possible.
As for enlarging existing holes, here’s how you play it:
- Clamp Some Scrap: Take some scrap wood and clamp it to your workpiece to provide a solid point on which to secure your drill bit.
- Mark the Centre: One of the problems with enlarging holes is the lack of a pilot hole. Mark the centre of the existing hole on the other side as you clamp your piece of scrap wood.
- Cut: With scrap wood securely clamped and marked, drill a fresh pilot hole into it and then continue as normal.
How to Care for Your Hole Saw
Knowing how to use your hole saw is one thing, but don’t forgo proper care. Here’s the low-down on cleaning, sharpening, and storing.
Cleaning
Regular cleaning extends the life of what can be a very expensive tool. After each use, clean your hole saw thoroughly to rid it of any dust or chippings. Left to their own devices, such detritus can become stuck or else damage the teeth – it’s worth keeping in mind that they’re very tough to sharpen once dulled.
It also helps to back the saw out occasionally while cutting to remove waste material and keep the blade cool. Apply even pressure as you cut to avoid tooth strippage.
Sharpening
If your hole saw should become dulled, the relatively low cost of replacing the blade should be enough to dissuade you from sharpening. If you’re set on sharpening, you can use a hand file on each individual tooth, though a hand-held electric grinder will slightly cut down on elbow grease. A bench grinder also does the job, but extensive time and concentration is required – honestly, it’s largely advantageous to replace instead of re-sharpen.
Storing
Finished with your latest project? Take a few minutes to see your hole saw properly stored if you want it ready to go next time round. It’s not too hard – simply store your hole saws in a dry place where they won’t be knocked about or corroded by the elements.
Safety Equipment When Using a Hole Saw
The chance of injury falls significantly when you don the right safety wear and employ the proper safety equipment. Hole saws don’t require much, but what they do require is vital.
- Eye Protection and Mouth Guard: To prevent dust or splinters getting in your eyes or being inhaled.
- Safety Gloves: To maintain proper purchase through cutting.
- Ear Protection: To safeguard your hearing while drilling for extended periods.
If working with any material save wood or cast iron, cutting oil or lubricant must be used to reduce resistance and extend the saw’s life. When using a more powerful drill to cut through a tougher material, the machine may experience ‘kick back’; under such conditions, you’re well advised to use a drill with a side-handle to afford additional stability and control.
Fix a Hole in Drywall
About: Build.Share.Destroy.Repeat. Follow me and try a few of my projects for yourself! About mikeasaurus »
Whether from a door knob, rambunctious kids playing, or a moving accident; a hole in drywall is an ugly eyesore. You might think that repairing this unexpected opening would require all kinds of specialized knowledge, but repairing a hole in drywall is actually very easy. Chances are, you probably have most of the stuff needed to make the repair at home already!
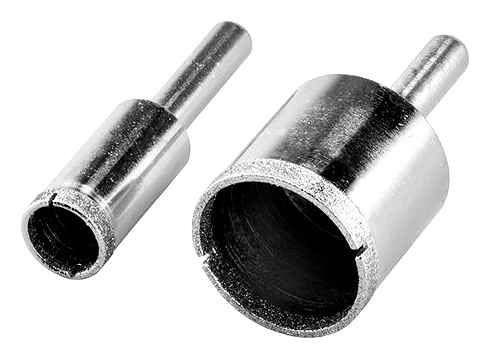
Step 1: Tools Supplies
To fix a hole in drywall we’ll be cutting a plug from around the damaged drywall and replacing it with a plug of undamaged drywall. To do this, we’ll use a standard hole saw of the right size. Hole saws are a useful tool and it’s worth getting a set that includes multiple sizes, rather than just one.
- Hole saws (buy a kit with multiple sizes)
- Electric drill
- Fresh drywall scrap (any thickness)
- Scrap plywood (any thickness)
- Broad putty knife
- Hobby knife
- Joint compound (also called “mud”)
- Sandpaper
The rest of the items on this list are what most homeowners should have lying around. If you don’t, then this is a good opportunity to get a few materials that will make home repair much easier the next time something like this happens.
Step 2: Size Hole Saw
We’ll start by matching a hole saw to the size of the damage in the drywall. Chose a hole saw that is as close a match in size as possible.
Step 3: Assemble Hole Saw
Once you have the size of the hole saw you need you’ll need to assemble the saw onto the threaded mandrel.
Every hole saw is a little different, but most will have a nut that needs to be removed before the hole saw is slipped onto the mandrel. In my hole saw, the opening in hole saws align with the asymmetrical mandrel and are seated fully before placing the nut back on and tightening, securing the hole saw in place.
Because hole saws are threaded in the same direction that the saw cuts, there’s no reason to over-tighten the nut since friction will self-tighten it. Therefore, hole saw nuts can be firmly hand tightened.
Step 4: Cut Plywood Template
To prevent the hole saw skipping around the drywall when cutting, there needs to be a template that will support the circumference of the saw blade. I used scrap plywood.
The scrap plywood can be of any thickness, since it’s only guiding the blade and keep it in place when cutting drywall.
Step 5: Drill Out Damage
Place the template against the wall, with the opening in the template directly over the damaged drywall.
Holding the template firmly against the wall with one hand, line up the hole saw inside the template and slowly drill and push into the drywall, the template will keep the hole saw centered around the damage.
Continue drilling until you cut completely through the drywall. A clean hole will be left, with a plug of the damaged drywall in the hole saw.
Remove the template, hole saw, and any debris in and around the opening.
Step 6: Make New Plug
To cover the opening in the wall we’ll make a plug of drywall using the same hole saw. A great benefit of using this method is that almost any thickness drywall will work to make a new plug, it doesn’t have to match the thickness of the existing drywall. If you have ½” thick drywall and a ⅜” thick sheet of scrap plywood then this method will work fine!
Keeping the drill perpendicular to the scrap piece of plywood, start drilling into the scrap but stop before going all the way through.
Your hole saw should have made it through the gypsum middle layer but not through the back paper layer. This is critical to patching the hole. If you accidentally drilled all the way through the scrap drywall find another area and drill a new plug. you’ll need the backing paper to make an effective patch.
Step 7: Cut and Score Patch
With a sharp hobby knife cut around the partially drilled drywall scrap. Take your time and make multiple shallow cuts to cut completely through the scrap drywall.
You’ll need a few inches around the partially drilled plug to make a patch.
Score radial markings from the partially drilled plug to the outside of the cut patch. The scoring doesn’t have to be very deep, just enough to allow the drywall to break apart with our hands.
With a firm grip break along the scoring and remove the drywall from around the partially drilled plug, being careful to leave the paper backing in tact.
A house under a stone with your own hands
When done correctly you’ll have a drywall plug with a skirt of paper attached.
Step 8: Trim and Wet Patch
Trimming the corners off the patch is optional, but I think makes the patch easier to conceal without any sharp edges. I used regular scissors to make a small radius on each corner.
Using a damp rag I moistened the paper of the patch. Don’t make the paper soaking wet, the idea is to have a moist paper patch which will accept the drywall compound mud.
Dab the paper with the damp rag, being careful to keep the moisture on the paper and not the drywall. Once wetted, set patch aside.
Step 9: Apply Compound to Opening
Open the drywall joint compound and mix thoroughly. Using the putty knife apply a generous amount of joint compound in the opening and on the surface around the opening.
Ensure there’s plenty of compound on the inside of the opening, this will be filling the gap made by the hole saw blade kerf. When the new plug is inserted it will squeeze any excess compound in behind the wall where it won’t be seen, so don’t worry about overdoing it here.
Step 10: Insert Patch
Line up the wetted paper patch and insert with the plug inwards, leaving the paper back facing you.
Gently press the plug into the opening until fully seated and the paper backing is flush with the wall.
Use the putty knife to press from the middle of the patch outwards to squeeze out any air bubbles and make good contact between the paper skirt and the wall. Any joint compound that is pushed out from the putty knife just place back on top of the patch and continue smoothing out.
Step 11: Add Joint Compound
Apply more joint compound with the putty knife over the patch, using the knife to smooth out the compound into even and smooth coats.
The aim here is to make a smooth transition from the existing surface of the wall to the edge of the patch. I find it’s effective to alternate and make passes from the center outwards, then go back from outside the patch and make passes in towards the center.
When the patch, and more importantly the patch edges, are covered allow the joint compound to dry completely. I left the compound to dry overnight before moving on to the next step.
Step 12: Sanding
When the joint compound is completely dry it can be sanded smooth. Attempting to sand partially dry joint compound will not work, and will make a huge clumpy mess.
Start with 120 grit sandpaper and work up to 200 grit sandpaper, removing the putty knife marks, high spots, and smoothing the joint compound to make a seamless transition from the existing wall to the patch.
After sanding clean up all dust and debris before painting.
Step 13: Paint
To cover the patch, matching paint was applied with a paint roller. Rollers are a better choice for painting large flat areas, not just because it’s faster, but the finish a roller leaves is much smoother than with a brush.
If your patch was near an outlet or switch, it’s best to remove the faceplate or mask with tape to prevent painting it accidentally. The more time spent on sanding the patch and joint compound to make a smooth transition will pay off after painting. Can you even tell where the patch is in the above picture?
Have you repaired a hole in drywall based on this Instructable? I want to see it!
People Made This Project!
Did you make this project? Share it with us!
Make It Bridge
Magnets Contest
Комментарии и мнения владельцев
You have a typo I think. Where you write “Keeping the drill perpendicular to the scrap piece of plywood, start drilling into the scrap but stop before going all the way through.” You write PLYWOOD, but for that step you mean DRYWALL instead, right?
Step 1: Tools (Torch/Flashlight, rubber glove), look into hole to see if any wiring or plumbing is in the vicinity, use rubber glove to feel around the inside for the same.
A friend was drilling a hole in the ceiling, the drill grabbed the wire, all he heard was this noise across the ceiling as the slack tightened, drill stopped, fell of the chair. bigger repair.
i like this approach, but have one question. the holes i’m going to patch were where the shower curtain rail was mounted. will this patch be strong enough for me to re-mount the shower rail on it?
No. The patch will be less strong than undamaged gypsum board. Perhaps you could make a decorative wood or metal piece that is larger than the current hole and put it over the hole (before or after you patch the hole) and then attach the curtain rod to that piece.
You can also make a wood mount for the rod
No. This will not work for any repair that will need to provide any kind of support. This instructable is a cosmetic patch only. What will need to be done for this repair to take any load, is to support the new piece of drywall from behind. To create the support you will place a length of wood a few inches longer than the hole is wide on the inside of the wall (generally the larger the piece the stronger). The piece of wood is then fixed in place using drywall screws (or similar) on each side of the hole. The filler piece of dry wall is the attached to the wood backer with another screw (add more for larger patch if needed. approximately 1 every 6 inches. Make sure the screws heads are a little recessed, but do not break through the surface (you should be able to feel this with you finger or trowel).
Note: The above steps are to be completed before applying any “mud”. If you don’t mind a little mess, you could apply the “mud” after the wood is in place, but before inserting the filler piece of drywall. If you choose to screw the drywall in place before “mudding”, you will just lift the edge to of the paper to wet it and to “mud” the wall.
The patch may then be finished as shown in this instructable (there are many ways to finish drywall. the method in this instructable is suitable for a beginner or those not wanting to buy additional tools). Hope this helps.
How To Cut A Hole In Lath And Plaster Ceiling?
Do you need to cut a hole in your lath and plaster ceiling but have no idea how to go about it? Don’t worry, you’ve come to the right place! Cutting holes in lath and plaster ceilings can be tricky, especially if you don’t know what you’re doing.
But with the right tools and a few precautions, cutting holes in your ceiling can be surprisingly simple.
In this article, I’ll walk you through the whole process from start to finish so you can create the perfect hole in your lath and plaster ceiling without any mess or hassle.
We’ll cover the materials you’ll need, safety tips, and step-by-step instructions on how to do it correctly.
By the end of this article, you’ll be an expert at cutting holes in your lath and plaster ceiling! Let’s get started!
Reasons for Needing to Cut a Hole in the Lath and Plaster Ceiling
If you’re looking to access wiring, pipes, or other hidden elements in your walls or ceiling, then you’ll probably need to cut a hole in it.
The tricky part is that many older homes have lath and plaster walls and ceilings, which are harder to work with than drywall.
Fortunately, with the right tools and safety gear, you can easily cut through lath and plaster.
But before we get into the how-to of it all, it’s important to understand why you might need to cut through this material in the first place.
- Installing new lighting fixtures
- Running additional wiring
- Cutting out old rotted ceiling material
- Replacing insulation around pipes or wires
- Accessing plumbing or electric elements behind walls or ceiling surfaces
No matter what your intended project is, know that cutting into lath and plaster is possible, and the end result will be worth it!
Preparing the Area to Be Cut
After obtaining your measurements and marking the wall, you should prepare for the next step.
Start by turning off the electricity to the area in which you’ll be working, just to be safe.
Then, use a utility knife around your marked area to cut through the plaster.
This will create a nice, clean line for you to follow when cutting your hole.
Next, use a handsaw or a reciprocating saw to cut along the line that you created with your utility knife.
You may want to use a piece of plywood underneath the area where you are cutting for added support, as lath and plaster can crumble with intense force or vibration.
While cutting through the lath and plaster, be sure to go slow and steady; you don’t want to crack or damage anything!
Once you have finished cutting, remove any remaining chunks of lath and plaster from around your hole so that it is smooth and even.
To finish up the job, wipe away any excess dust using a damp cloth before handing over the job to an electrician if needed.
Choosing the Best Tools to Use
When it comes to cutting a hole in lath and plaster ceilings, the right tools for the job can make all the difference.
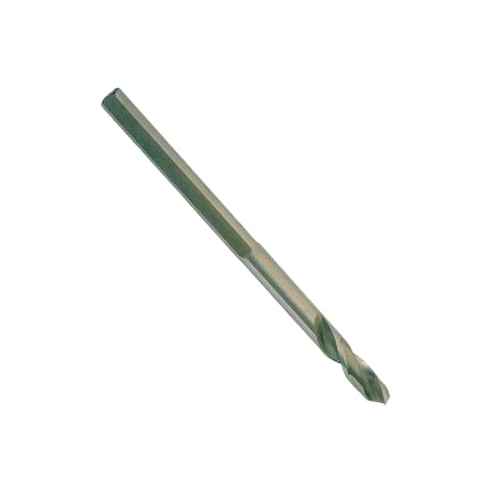
When starting out, you should consider some of the top tools.
Compound Miter Saw
For making precise cuts, you can’t go wrong with a compound miter saw. This power tool is ideal for cutting accurately sized holes in lath and plaster ceilings because it provides a level surface for your saw blade to sit on as you work.
Circular Saw
Circular saws are another great option for cutting into lath and plaster ceilings, especially if your hole size isn’t very large.
Make sure that your circular saw has a dust collection port to help keep your workspace clean as you work.
Power Drill and Hole Saw Attachment
If you need to cut a larger hole than a miter saw or circular saw can handle, then using a power drill combined with a hole saw attachment is the way to go.
You can use a hole saw to cut larger diameter holes quickly and efficiently for any size job you need to complete.
Make sure that the size of the hole you cut is smaller than the width of the lath strip, to avoid weakening the lath too much.
Cutting the Hole in the Lath and Plaster Ceiling
Now it’s time to get down to business and cut the hole in your lath and plaster ceiling. To begin, gather a few tools, such as:
- A drill with a spade bit
- A hammer
- A jigsaw or keyhole saw
- Safety gear (safety glasses, a dust mask, and hearing protection)
Once you have all your gear together, here are the steps to take:
- Before beginning, ensure that you wear your safety gear.
- Drill a hole in the ceiling using the spade bit. This step helps you draw out a rough outline of your hole.
- Using the hammer, gently tap away at any large chunks of plaster that you can easily identify on the ceiling. Don’t use force as it will cause cracks in other parts of the ceiling and walls!
- Insert the blade of your jigsaw or keyhole saw into one edge of the hole outline that you previously drew and slowly cut out the area around it; pay attention not to overdo it just in case you need to patch up some areas!
- When finished cutting, remove any loose pieces from inside your newly created gap from lath and plaster by vacuuming them away. Be careful not to remove too much since this can weaken any surrounding areas!
With these steps in mind, you should now have successfully cut out a safe and secure gap for whatever project needs attention on that part of the lath and plaster ceiling!
Dealing With the Debris From Cutting the Hole
Once you’ve cut the hole in your lath and plaster ceiling, you need to deal with the mess that was made.
Cleaning up the debris is an important part of the process and something you should take seriously.
Here are some tips to ensure that you remove all of the debris:
- Use a Shop-Vac to suck up all of the dust and small pieces of plaster that have been created by cutting through the lath and plaster ceiling.
- Use a broom and dustpan to sweep up any remaining debris from around the hole in your ceiling.
- Vacuum any remaining pieces of dust or debris from the floor around your work area, as this will help keep your home free from potential health hazards.
- Wear a dust mask to protect yourself from any particles that may still be floating in the air after cleaning up your mess.
- Dispose of any material safely, and properly recycle any plastics or metals that may be included with your lath and plaster materials.
Finishing Off and Ensuring Safety
Cutting a hole in lath and plaster is a delicate operation, so it’s important to take safety measures to ensure that the job is done safely and securely. Here are a few things you can do:
Wear Protective Gear
When cutting lath and plaster, you should always wear protective gear like eye protection, gloves, a dust mask, and long sleeves.
This will help protect you from flying debris when cutting the lath and plaster, as well as any toxic particles that may be released.
Secure the Ceiling
It’s also important to secure the ceiling before drilling into it. This includes removing any hanging light fixtures or wires, bracing the area around the hole with wood planks (to prevent anything from falling through), and covering the floor beneath with plastic sheeting or a dust sheet.
Finally, ensure that you’re using a sharp drill bit that won’t get stuck in the lath and plaster.
Once everything is organized and in place, start drilling slowly and steadily. You should work your way around the perimeter of the hole to make sure it is accurately sized for whatever object needs to fit through it. Then clean up any debris from the floor before moving on to patching up the ceiling.
Conclusion
To master the art of cutting a hole in lath and plaster walls and ceilings, the most important thing is having the right tools and taking the necessary safety precautions. With the right knowledge and know-how, you can confidently tackle the task ahead, either on your own or with a team.
Cutting a hole in a lath and plaster wall or ceiling doesn’t have to be an intimidating task, so long as you take the necessary steps to ensure that you’re cutting safely. The results can be spectacular if you take the necessary time to measure and plan accurately, as well as equipping yourself with the tools and skill set to achieve the best outcome.
FAQS
What tools do I need to cut a hole in a lath and plaster ceiling?
Tools needed: drill, saw, knife, tape, pencil, ladder, goggles, and a dust mask.
How do I locate the ceiling joists before cutting the hole?
Locate ceiling joists with a stud finder or by tapping; mark with a pencil before cutting the hole.
How do I cut the hole in the ceiling without damaging the surrounding plaster?
Drill a small hole in the center, use a saw to carefully cut around the edge, score the plaster with a knife to prevent cracking, remove loose plaster, and clean up debris.
About Charlie D Paige
Charlie is a massive DIY fan, with dozens of DIY projects under his belt. ranging from tiling to electrics, and concrete pads to walls. Charlie loves tinkering, seeing how things works, the outdoors and playing with power tools. so is it any wonder that he’s completed so many DIY jobs over the years?
Charlie loves spreading his hard-won DIY experience with the world via this blog.
About Charlie
Hello! I’m Charlie Paige, a housing and DIY enthusiast. A quality home life is essential to all of us, so I wanted to build this blog to help others improve their houses. Read more.
How To: Cut Plaster Walls
Yes, there are times when you need to cut a hole in a plaster wall. And before you do it wrong and knock big chunks of plaster from your walls or ceilings, I thought I’d give you some tips on how to cut plaster walls the right way.
I see tragically destroyed original plaster walls all the time. Usually, the damage is courtesy of a hurried plumber or electrician who doesn’t care since they aren’t the ones patching the holes.
I will warn you that cutting through nearly 1″ thick plaster is not without its messes. It is a dusty job and you can’t always be sure to avoid all the crumbling plaster, but with the right techniques, you can avoid most mishaps.
The Wrong Tools
Plaster and wood lath are extremely sensitive to vibration. Lots of shaking and vibration can cause a chain reaction that will bring a whole ceiling crashing down.
Cutting plaster without disturbing the rest of the wall requires tools that are more surgical and less shock and awe.
Unless your plans are for massive demolition, stay away from the following tools when it comes to cutting plaster.
The Right Tools
High speed tools work best to cut through plaster smoothly. They don’t cause the lath behind to bend and flex knocking other things loose which is what you want to avoid.
High speed tools cause much more dust than other tools, so make sure to use a HEPA vacuum with them or keep the surface moistened, both of which help control dust and protect you.
If your walls or ceilings get a positive test for lead paint make sure you follow lead safe work practices! Always wear an appropriate respirator when cutting plaster.
Use the following tools for surgical like precision when cutting plaster.
How to Cut Plaster
Cutting plaster is not extremely difficult with the right tools, but it does make a mess so be ready with containment and cleanup. For larger areas, I use an angle grinder with a diamond blade since this can go pretty fast. For more fine tuning or for smaller cuts, I prefer the multi-tool.
Step #1 Mark Off Your Cut
Use painter’s or masking tape to mark off the areas you are going to be cutting and draw your cut line on the tape. The tape will help keep some of the crumbling plaster from falling out in the middle of your cut if there is any and it helps you see what you are cutting.
Step #2 Make Your Cut
Using either the angle grinder or multi-tool cut along your line. Make sure to finish the cuts all the way to the end so that all the lines connect. Be sure to cut all the way through the wood lath behind.
Step #3 Remove the Patch
If you’ve cut all the way through the lath, the patch should fall right out as you make your last cut. Take this time to clean up anything necessary keeping in mind that the hole doesn’t have to be perfect since it will likely be covered with a switch plate or some other escutcheon for the item you are installing.
Step #4 Cleanup
Vacuum up any remaining dust and wipe the wall down with a wet cloth to get the remaining plaster dust off.
Maybe you’re not the one doing the cutting, but these practices are still important to tell anyone working on your house since you’ll be the one patching it up.
With a little knowledge and practice, we can save antique plaster walls all across the country!
Total Tools. Low Price Guarantee Policy (Terms Conditions)
At Total Tools we offer Low Prices, every day, guaranteed. We will not be beaten!
We check our daily against our competitors to ensure you can shop online or instore with the confidence you are buying at the very best price, every day.
Should you find a lower advertised price for the identically stocked product elsewhere, we will happily match the price. [Subject to Terms Conditions – see below for details]
At times have moved in the market, and our in store and online price for printed catalogue items may be lower. Check online or instore for the latest price.
How to Price Match
Simply visit a Total Tools Store or contact our online team with evidence of a cheaper price (print out or website link). We will verify the price, and then immediately match any current advertised price (Terms Conditions apply).
Terms Conditions
For eligibility, the following terms and conditions need to be met;
- Product must be identical (same brand, colour, model #)
- Product must be currently advertised in print or electronic media (Including newspaper, catalogue, radio, television advertising or online)
- Product must be in stock at the competitor
- The competitors price of the product must be inclusive of delivery fees, taxes and charges
- The competitors price is lower than our price on the day the price guarantee is requested (day of purchase)
- The competitors price excludes finance, installation, bundling, rebates, cash back, coupon offers, loyalty rewards or free bonus goods.
- The competitor is located in Australia
- Trade/commercial quotes and/or large volume/bulk purchases
- Products for sale via auction, stock liquidations, fire sale, sale or clearance (including eBay)
- Blemished, seconds, refurbished, damaged or ex demonstration stock
- Advertising errors where competitor has published a rectification notice
- Products distributed by unauthorised dealers / parallel importers
- Special event, club or membership offers, third party promotions or not available to the general public
- Special order products
Total Tools reserve the right to terminate or amend the price guarantee policy at any time without notice.
For Further Information
Further information may be obtained in-store at any of our stores nationwide or online at www.totaltools.com.au/priceguarantee. For the most effiicent response please use the contact us page, or alternatively email onlinesupport@totaltools.com.au.
GET TO WORK NOW, PAY LATER Click to see your options
Love tools? Start earning points to redeem rewards on your next purchase Log in or Sign Up to redeem today!
Pickup In Store
If you don’t want to pay for delivery or need to ASAP, you can pick it up in store. Just bear in mind not all stores will have everything in stock. You’ll be able to see if they do during the checkout process.
Free Delivery
Most products are included in free delivery, however some are excluded as follows:
- Orders and/or items under 99.
- Orders and/or items that are deemed bulky, large or heavy.
- Clearance items.
- Orders that include or items that are classed as dangerous goods.
- Remote areas are excluded from free delivery and you will either be charged delivery at checkout or may be contacted prior to delivery to confirm delivery charges if necessary.
- Interstate deliveries.
Total Tools reserve the right to change or withdraw free delivery at any time.
Estimated Delivery Timeframes
If you opted to collect in store you will receive an email to inform you when your goods are ready for collection.
If you opted for delivery, you will receive an email when the goods have been despatched to the couriers with details so you can track our order.
We aim to despatch all orders within 1-2 business days. In the unusual event of a delay to the despatch of your order you will be contacted at the earliest opportunity. Once the order has been despatched the estimated delivery time is as follows:
- Metro (Excludes Hobart Metro) 1-2 business days
- Hobart Metro 3-4 business days
- Regional Areas 3-4 business days
- Remote Areas 6-9 business days
Please note that these delivery timeframes are estimates and are not guaranteed.
Returns
Changed your mind? No worries. You just need to get the product back to the store it was shipped from (this is on your receipt) within 30 days, unused and in its original packaging and we’ll give you a refund (excluding delivery costs). You can read our full returns exchanges policy here (special order items are excluded from this returns policy).
Total Tools. Low Price Guarantee Policy (Terms Conditions)
At Total Tools we offer Low Prices, every day, guaranteed. We will not be beaten!
We check our daily against our competitors to ensure you can shop online or instore with the confidence you are buying at the very best price, every day.
Should you find a lower advertised price for the identically stocked product elsewhere, we will happily match the price. [Subject to Terms Conditions – see below for details]
At times have moved in the market, and our in store and online price for printed catalogue items may be lower. Check online or instore for the latest price.
How to Price Match
Simply fill in price match form available on every product page or visit a Total Tools Store. We will verify the price, and then immediately match any current advertised price (Terms Conditions apply).
Terms Conditions
For eligibility, the following terms and conditions need to be met;
- Product must be identical (same brand, colour, model #)
- Product must be currently advertised in print or electronic media (Including newspaper, catalogue, radio, television advertising or online)
- Product must be in stock at the competitor
- The competitors price of the product must be inclusive of delivery fees, taxes and charges
- The competitors price is lower than our price on the day the price guarantee is requested (day of purchase)
- The competitors price excludes finance, installation, bundling, rebates, cash back, coupon offers, loyalty rewards or free bonus goods.
- The competitor is located in Australia
- Trade/commercial quotes and/or large volume/bulk purchases
- Products for sale via auction, stock liquidations, fire sale, sale or clearance (including eBay, Amazon)
- Blemished, seconds, refurbished, damaged or ex demonstration stock
- Advertising errors where competitor has published a rectification notice
- Special event, club or membership offers, third party promotions or not available to the general public
- Special order products
Total Tools reserve the right to terminate or amend the price guarantee policy at any time without notice.