DIY Table Saw Table. Table saw extension diy
How to make cast iron table saw router table extension fit?
I have the cast iron table top from this router table (also the stand, but never mind):
It isn’t exactly the right size to take the place of one of my Craftsman 315.22830’s table saw extension wings, but making it fit isn’t a complicated engineering problem (i.e. I’d just add some wood).
My question is how to attach it. I can drill and tap holes in the right places to line up with the cast iron table in my saw, but will attaching it the same way the steel ones are attached work. or will it just fall down? They’re just held in place with bolts along their inside edges a little extra support from the fence rails.
This thread has a picture of a different Craftsman table saw (scroll down a little). mine doesn’t have the iron wings with cutouts. but it’s the same idea:
nickbatz
This is a different (older) table saw and the cast iron extension wings aren’t solid, but the left wing seems to be attached by bolts only and it works.
Bob5103
When I had my cast iron router table in the table saw I used 2 adjustable legs on the out board side. Looks like Grizzly sells the sells the legs
bigJohninvegas
So I added a cast iron router table to my Ridgid r4512. Pretty easy actually. The cast iron top on your saw should already be tapped, while the stamped steel wings have holes drilled. I just drilled the cast iron wing to match the holes in my saw. and also dilled the router wing to match the rails on my fence. So the router wing is attached on 3 sides. Most table saws are 27″ deep. The MLCS web site shows the top you are using to be 26-7/8″. so you may need a little shim. Originally I had upgraded the two stamped steel wings and the fence. My one and only blog post covers it. Then a couple years later I bought a saw stop cast iron router wing, and switched it with one of the earlier cast iron wings. I have some photos, and thought I had a post on it, but I can not find one. I’m not the best at posting my own projects and such. So apparently I never got around to it. But I do have photos.
This photo shows lining up the holes in the saw. Cast iron is very easy to drill. I find most cast wings come with 4 holes, where saw with stamped steel wings only have 3 holes.
I had added a biesemeyer commercial fence with the original wing upgrade. So I have an angle iron rail on front and back. You can see two bolts on front rail. Same on back. This give plenty of support. No sagging at all. Seven bolts total. I think if you bolt yours up in the same fashion, it will be fine. the original fence on my Ridgid saw had a two piece aluminum front rail. I had added a angle iron rail under it because it never stayed straight to begin with. I do feel if I had not upgraded my fence. I could have still attached the cast wing to the factory fence, and had plenty of support.
nickbatz
John, what do you use to drill cast iron. any special bits?
Thinking about it, I may be able to support it on the inside using metal strips. Will have to look. The 16″ extra on each side might be just enough room.
nickbatz
Bob, I have the stand for the table. I’d like to be able to this without using legs, since convenience and saving space are the whole point.
bigJohninvegas
John, what do you use to drill cast iron. any special bits?
Thinking about it, I may be able to support it on the inside using metal strips. Will have to look. The 16″ extra on each side might be just enough room.
Nothing special, any bit for metal will.work fine. Cast iron is a soft metal. Just make sure youbuse a center punch, and be as accurate as possible. I had to over size my holes a little more than I wanted. But with the added bolts in the fence. It has never moved.
nickbatz
Nothing special, any bit for metal will.work fine. Cast iron is a soft metal. Just make sure youbuse a center punch, and be as accurate as possible. I had to over size my holes a little more than I wanted. But with the added bolts in the fence. It has never moved.
WoodenDreams
I just added a Grizzly T1244 cast iron router extension wing to my table saw https://www.grizzly.com/products/grizzly-router-table-wing-for-table-saws/t1244
D.I.Y Build a Table Saw Extension Table
I attached it flush with the front rail and table. It was supposed to be 27″ length, same as my table surface (front to back). It was 1/8″ shorter, so I used fender washers as spacers to keep the back rail straight. Drilled holes as needed. Cast iron drills easily. If you drill the holes larger than needed for the bolts, it will allow for fine tuning (up or down movement) to get a flat surface. once on, and you match the level to the table surface, use a straight edge to check for flatness. If outer wing is lifted up, loosen up the bolts and add a strip of painters tape to the connecting edge. Will act as a shim to lower or raise the edge of the wing for a level surface.
Adding a cast iron wing to one side, may make your table saw tippy. You may need to add a leg or two. Legs are available as Bob5103 says. You can make your own legs with wood
MPython
My cast iron extension table attachment is similar to BigJohn’s. I bought a SawStop ICS to replace my Unisaw with the intention to move the the Bench Dog table extension from the Uni to the SawStop. There were two problems with that plan: The SawStop table is 3″ wider than the Uni’s table and the mounting holes in the Bench Dog extension table didn’t line up with the mounting holes in the SawStop. I marked the location of the holes in the table onto the extension and took it to a local machine shop and had them mill new holes to match the SawStop mounting holes. The milling was not as clean as I’d hoped and it left me with what appeared to be a pretty flimsy mounting bracket on the table extension. I was able to secure it solidly to the SawStop table with bolts and some large washers. The 27″ wide extension left 1 1/2″ gaps on either end when mounted to the SawStop and I was unable to secure it to the SawStop’s heavy angle iron fence rails. I used it that way for a couple of months without issue, but I was afraid the compromised mounting bracket in the extension would eventually fail. I filled the gaps with some heavy (1/4″ thick) extruded aluminum square tube and secured the ends of the extension to the tube and the tube to the saw’s fence rails with large threaded machine screws. The result is a rock solid assembly that has withstood a lot of use and weight over the last 4 or 5 years. I’m not sure if the extension table would have endured had I not secured it to the fence rails. Here’s a photo, FWIW:
bigJohninvegas
I just added a Grizzly T1244 cast iron router extension wing to my table saw https://www.grizzly.com/products/grizzly-router-table-wing-for-table-saws/t1244
I attached it flush with the front rail and table. It was supposed to be 27″ length, same as my table surface (front to back). It was 1/8″ shorter, so I used fender washers as spacers to keep the back rail straight. Drilled holes as needed. Cast iron drills easily. If you drill the holes larger than needed for the bolts, it will allow for fine tuning (up or down movement) to get a flat surface. once on, and you match the level to the table surface, use a straight edge to check for flatness. If outer wing is lifted up, loosen up the bolts and add a strip of painters tape to the connecting edge. Will act as a shim to lower or raise the edge of the wing for a level surface.
Adding a cast iron wing to one side, may make your table saw tippy. You may need to add a leg or two. Legs are available as Bob5103 says. You can make your own legs with wood
Using fender washers for shims is a great idea. I was going to suggest shimming the back side and setting the table flush with the front. I was lucky in that the saw stop wing was a true 27″ wing. and I like your idea of using a strip of tape as a shim if needed. I got lucky there too, and did not need any shimming. I did have some angle iron from the original fence. I you look at the blog post link in my earlier comment you will see photos of the angle iron I used it when installing the wings. clamped it to the saw top. I was working alone, and very hard to handle the heavy wing and start the bolts at the same time. So I loosely clamped the wings to the angle iron to get the bolts started. Then tightened all the clamps just before I snugged all the bolts tight.
My question is how to attach it. I can drill and tap holes in the right places to line up with the cast iron table in my saw, but will attaching it the same way the steel ones are attached work. or will it just fall down? They re just held in place with bolts along their inside edges a little extra support from the fence rails.
This thread has a picture of a different Craftsman table saw (scroll down a little). mine doesn t have the iron wings with cutouts. but it s the same idea:
Nick, I looked up the model number on your saw and did not find it. and you mentioned the saw shown in the link was not the same saw. Is your saw an older model? they made a saw that was pretty much a clone to my ridgid R4512 saw. If you look at the photos I posted. You can see the hole in my table at far right. When I upgraded to the 52″ fence, I added my router lift there. even without the lift, the saw would have been tippy with the long rails. and it came with legs just because of that. With the long rails, my saw became the only tool in my shop to be in a fixed location. Although the mobile base will still pick it up, but you have to control it from the right end. (That end stays on the ground now until you go and handle it) Before the long fence, it was a 36″ factory set up. I did have the router lift in a home made extension on the right side, that only stuck out about 3″. when the saw was on the ground, no mobile base in use. It was as solid as a rock. No legs needed, but when you pick it up to move it. It would sit ok, but I had to drive it around from that right side. It would try to tip if you were moving it without controlling it from that end. So be aware of that. Once I added the long rails, and my saw became a stationary tool. The lift no longer worked in that end with my shop set up. Did not see it when I set it up that way. So when I went with the cast iron router wing. I was planning to put it on the left as it is now. But that came with a huge challenge. the motor housing sticks out, and just barely clears the router itself. And I had to cut a fine out of the vent to bolt the wing up. Such a tight fit that I had to build a custom allen wrench tool to get it done. I have no idea what the under side of that MLCS table looks like. The support ribs are different on them all. But the opening for my router lift made the center hole almost imposable.
And with the housing sticking out, and regular hex bolt was and issue too. so I cut a fin out of the motor housing, and cut a allen wrench.
Build this take-down table saw table to make the perfect work station for a DIYer with limited garage space.
Family Handyman
Introduction
This DIY table saw table is the perfect solution for cutting long boards or big sheets of plywood. It’s also a handy workbench with storage trays. When finished, a DIYer can quickly dismantle the table saw table and store it flat against a wall, saving valuable garage space.
Materials Required
DIY Table Saw Table Overview: A Knockdown System Without Fasteners
Portable table saws are great for garage workshops. When the project is done, they fold up and tuck away so you can park the car. But when it comes to capacity, they’re a bit limited.
That’s what led to this knockdown table saw system. It has a great outfeed table; you also gain extra width to rip larger pieces of plywood, and the outfeed table works great for an assembly workbench. The project also has some nifty add-on trays: one to hold your table saw safety equipment (hearing and vision protection and push sticks) and another to hold all your hand tools and hardware so you can keep the top clutter-free. This project is perfect for a small workspace because it sets up in minutes without fasteners, and at the end of the day, you can have it back on the wall and the car in the garage.
DIY Table Saw Table
Family Handyman
This DIY table saw table is a workshop on a wall. In less than five minutes of setup time, you’re ready to cut big sheets or work on the assembly table.
With these jigs and accessories, you can make safer, more accurate rips, crosscuts, dados, rabbets cuts and more.
Gather Materials and Begin Cutting the Table Saw Table Parts
Family Handyman
This project requires four sheets of 3/4- in. plywood. The side panels (A) and end panels (B and C) are each cut from a separate sheet of plywood. It’s best to cut the outfeed top (G) from the same sheet as the outfeed end panel (C). From the leftovers, you’ll have more than enough scrap to cut the struts, supports and feet, plus any trays you choose to build.
We used hardwood plywood (oak). Stay away from construction-grade plywood (it’s usually labeled “A-C”, “B-C” or “C-D”). Construction plywood is cheaper and tends to warp and is difficult to cut cleanly.
If you’re building this project for a portable saw with its own cart, set up the saw and measure the height of the saw top down to the floor. Subtract 3/16 in. from this measurement and make parts A this height. Part B, the front panel, should be 3-1/4 in. shorter than A. The back, part C, can remain the same as in our plan. It’s important to have the top of the surround just slightly lower than the table of your saw to ensure the workpieces don’t get caught on an edge as you cut. If you’re fussy about setup, you can shim under each foot to dial in the exact height.
After adapting parts A and B, you can use the Cutting List found in “Additional Information” below to cut the other parts. Check the two sides of your plywood before cutting. One side may be darker than the other. We planned our cuts so all the lighter sides would face out. This not only looks good but makes assembly easier.
Cut the Notches
Family Handyman
This project assembles with interlocking notches, so cutting the slots accurately is a must. You want the notches to be about 1/32 in. wider than your plywood. This “play” in the notch makes for easy setup and knockdown and still gives sufficient rigidity. The depth of each notch needs to be exact so that the tops of all the parts line up and give you a flat work surface.
Before cutting notches, set your saw depth and make a test cut to check the depth. Screw a block to a sawhorse and clamp the sides (A) precisely together to hold the parts upright and cut. For each notch, make several cuts no more than 1/8 in. apart. Cut out thin strips of plywood with a sharp chisel and smooth the bottom of the notch with a file.
Making a Portable Sliding Table Saw Attachment/Transformation of a Dewalt Table Saw/Expansion fence
Cut and Assemble the Sides
Family Handyman
Nail a strip of wood to a scrap of plywood or OSB, 12-1/2 in. from the edge of the scrap. Next, trace and cut the arches in the bottoms of parts A, B and C. Parts A are 30-in. radius and parts B and C are 24-1/2-in. radiuses. Cut the arches with a jigsaw. The curves add to the overall appearance of the project and also make the parts lighter and easier to handle. To complete the sides (A), glue and nail the 3/4-in. x 3/4-in. cleats (D) above the rear notches.
Cut and notch the struts (E) for the outfeed table. Then glue and nail the supports (E2) to the inner sides of the struts.
Assemble the Feet
Family Handyman
Cut the small plywood parts (F1 – F6) as shown in Figure A. For strength, use glue plus nails or screws, making sure the edges align and sit flat. After assembly, round over the outer corners with a belt sander or jigsaw. Be sure to remove any oozing glue.
Build the Outfeed Table
Family Handyman
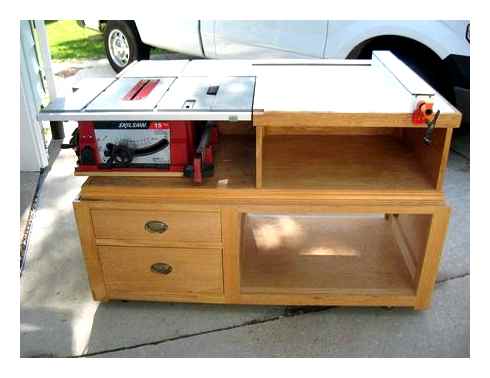
With the feet supporting the sides and the front and rear panels, lay in the struts of the outfeed table. Waiting to glue and nail the plywood top (G) until now will ensure that the struts will be in just the right spot and won’t bind during setup and knockdown. Glue and nail the top to the strut supports.
Check the interlocking joints to make sure they all meet at the right height and that no part of the outfeed table is proud or short of the sides. Also, make sure the front panel (B) is flush with the sides. If any of the notches fit too tightly, widen them with a file. If any are too deep, glue a thin shim into the base of the notch.
Now you’re ready to drill holes, some for trays and others for hanging the parts on the wall. I drilled 2-1/2-in. holes 16 in. on center to align with wall studs and drove 1/2-in. lag screws into the studs. Drill the holes with a hole saw. To get clean holes, start the holes from one side, then, as soon as the pilot bit emerges through the opposite side, remove the drill and finish the hole from the other side.
With the whole project complete, I rounded the edges of the parts with a 3/8-in. round-over router bit. This makes the whole project look better and reduces splintering on the edges, but it’s not mandatory. Then I sanded the plywood with 150-grit sandpaper, vacuumed, and applied two coats of Minwax Wipe-On Poly to all the parts. The finish will reduce warping as the humidity changes. Plus, it makes the whole project look great.
Make Your Table Saw Bigger With These 3 Tips
There comes a time in every woodworker’s life when your table saw surface isn’t big enough to cope with a job you’re doing. Short of buying a new table saw, how can you make the saw bigger to safely make the cuts you need?
I recall the first table saw I bought over 30-years ago. I was so proud of it, but the table was so small. Excellent for small cabinet-making jobs, but when I was renovating the various houses I lived in then, it was not good to rip a long board or cut a full-size sheet in half. I quickly learned what not to do if I wished to cut safely and accurately and keep all my body parts intact.
In this article, I’ll run you through two temporary methods to safely make your table saw bigger, then talk about a more permanent solution. First, let’s talk about the two most common scenarios you can encounter.
Problem #1 – Timber Outfeed Support
When we speak of infeed and outfeed on a table saw, we refer to the timber movement in relation to the blade. As we push a single piece of wood onto the blade and begin cutting, that’s the infeed side.
After the cut, the now two pieces of wood pass the blade, moving toward the rear of the table. That portion to the rear of the blade is called the outfeed side. The area to the rear of most table saws provides sufficient support for small pieces of wood, but as you begin to cut larger pieces, they will protrude over the back edge of the outfeed table.
Safety Note! If the wood is too long, the weight of the wood hanging over the back of the table is more than what you have remaining on the table, and it tries to lift the infeed end of the wood.
Such a situation is dangerous, as you find yourself leaning your weight on the small piece of wood left on the table to provide a counterbalance. It rapidly becomes impossible to continue feeding the wood while keeping the wood flat on the table. If you’re lucky, your knee can find the off switch, and you hold the timber still until the blade stops. If you’re unlucky, the blade jams, and you get a violent kickback, potentially doing you damage and certainly damaging the timber you were cutting. Don’t ask me how I learned this.
Problem #2 – Large Sheet Side Support
There is a limit beyond which the rip fence will not extend on small table saws. If you wish to cut larger sheets, you need to remove the rip fence, but if you’re cutting the top off an 8′ x 4′ sheet, you can have the best part of 7 feet of sheet hanging off to one side of the table saw. Even if you manage to feed the sheet evenly, which I doubt, you will certainly tip a small table saw on its side with the overhanging weight of the sheet.
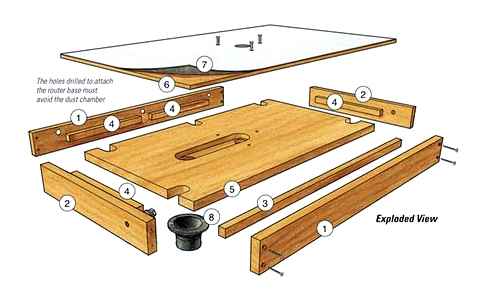
How then do you provide the support necessary to allow a smooth and accurate cut? The problem is the same as you have with the outfeed support, except this time it’s off to the right (or left if your saw is set up for left-handed operators)
Temporary Solutions
If you plan to be cutting timber that will overhang the tabletop, you need to provide an extension to the outfeed to safely support the wood at the same level as the tabletop. You have a couple of options.
The first solution is to use adjustable trestles. You have two possibilities with these. You can use them individually and adjust them to the level of the saw table to allow the wood to transfer onto them after leaving the back edge of the table or slide across the top if supporting a sheet to the side. Otherwise, you can use two of them to create a temporary table extension by clamping some ply to them and adjusting the trestles so that the top of the ply sits level with the table saw top.
What is Rip Capacity on a Table Saw? (What You Should Know!)
In this post, I’ll explore everything you should know about rip capacities and why it’s important. Let’s dig in!
- Rip capacity refers to the distance between a table saw’s blade and its fully extended rip fence. A wide ripping capacity allows the saw to cut larger sheets and boards such as plywood or other large pieces.
- A table saw’s ripping capacity can be extended with specially designed table extenders or a homemade tabletop extender if necessary.
What Is Rip Capacity?
The distance between the table saw’s fully extended fence and its blade is referred to as the saw’s rip capacity. In other words, rip capacity is the maximum material width that a table saw can handle.
Table saws are known for their ability to make precise rip cuts, but rip capacity affects the saws ability to make crosscuts, miter cuts, and bevel cuts too.
Virtually all modern table saws have a finite rip capacity, but that doesn’t mean you couldn’t add on your own extension, provided you have the materials, tools, know-how, and space necessary to do so.
That said, the majority of modern table saws are built to accommodate an increase in cutting capacity, and many even come with extenders that are durable, sturdy, and easy to attach.
Common Rip Capacities
There are a variety of table saws these days, and larger table saws have more rip capacity than smaller table saws.
But table saw rip capacity isn’t limited by the table’s size.
After all, a material’s width can exceed the capacity of a table, in which case you’d have a section of the material floating as it passes through the table saw’s blade at the opposite end.
Benchtop table saws, contractor table saws, and cabinet table saws are the three most popular table saw variants, and they all have different rip capacities.
Benchtop Table Saws (28 Inches)
Most benchtop table saws have a rip capacity of 28 inches. Models that come with extenders can have up to 48 inches of rip capacity.
Benchtop table saws are highly portable and great for smaller workshops, but most aren’t built to handle wide, heavy-duty materials regularly.
That said, if you need to cut a wide piece of medium-density fiberboard (MDF), and all you have is a benchtop table saw, don’t let the saw’s size discourage you, especially if it came with extenders.
In the worst case, a small section of the material hangs off the end, but this won’t really matter so long as the material is thick, dense, and run smoothly through the blade.
Note: These are the best table saws for small-time woodworkers who undertake a handful of woodworking projects each year.
Contractor Table Saws (30 Inches)
This table saw’s rip capacity is larger, but not by much. However, you can extend the rip capacity on these saws too.
The maximum rip capacity on most contractor saws is 30 inches, and usually extenders will add 10-20 inches.
Contractor table saws have greater rip capacity in large part because they’re designed for professional contractors.
Cabinet Table Saws (50 Inches)
Cabinet table saws, otherwise known as cabinet saws, have the most rip capacity, in large part because these saws are designed for frequent cutting of heavy-duty materials.
Along with having the most rip capacity, they’re also the largest table saw variant. Therefore, if your workshop doesn’t have a lot of floor space, think twice before getting a cabinet table saw.
Also, if you’re not doing commercial woodworking, metalworking, etc., then there’s really no need to have something as large and powerful as a cabinet table saw.
What Size Rip Capacity Do I Need?
To determine what size rip capacity you need, ask yourself the following questions; your answers will point you towards an ideal rip capacity.
How often do you cut wide materials?
If you don’t cut wide sheets and boards regularly, then you won’t need a table saw with a higher rip capacity. In fact, having a lot of rip capacity can actually be a hinderance when you’re working with small pieces of wood or another material.
That said, there may be times when you do need to cut wider materials, and when these times come it’s best to have extenders ready to go; this way you can increase rip capacity when you need to and shorten it right after.
Do you have space for a table extension?
The space around your table saw should be considered as well. If you don’t have a lot of space, it doesn’t make sense to get a saw with a lot of rip capacity; in this case the saw would be bulky more than anything else.
Does price matter?
Price should also be considered when you’re determining the rip capacity you want from a table saw.
Generally speaking, table saws with more rip capacity are more expensive. That said, there are plenty of mid-priced table saws with decent rip capacity, and if you find that the capacity on such a saw isn’t enough, simply add an extension.
Rip Capacity vs. Table Saw Cutting Depth
Sometimes rip capacity and cutting depth are referenced together as if they’re the same thing, but this isn’t the case.
Whereas rip capacity refers to the distance between the table saw’s rip fence and its blade, cutting depth refers to the maximum depth a table saw can reach when cutting through material.
In other words, if a table saw has a cutting depth of 2 inches, it can make cuts that are 2 inches deep (or thick) in a material.
Cutting depth is largely determined by the size of the saw blade. Most table saws use 10- or 12-inch saw blades, and 12-inch blades can cut deeper.
Material density is also relevant when considering a table saw’s cutting depth. Specifically, it’s harder to make deeper cuts in dense materials, like hardwoods and certain metals.
Can You Increase Rip Capacity on a Table Saw?
Yes, any table saw’s rip capacity can be increased—in theory. There are, however, times when rip capacity can’t be increased, like when there’s not enough free space around the saw to allow for this.
But most of the time, a table saw can be extended in one of the following ways:
Extend the Table
Most modern table saws come with tabletop extenders, and those that don’t can usually accommodate manufactured extenders.
Manufactured extenders are preferred over homemade table extenders for a few different reasons.
For one, they usually lock into place, making them sturdier and safer.
Also, since they’re made of the materials that modern table saws are made of, you don’t have to worry about the combined surface being multi leveled.
But these extenders cost more than homemade versions, and you may have a hard time attaching an extender, especially if it wasn’t made specifically for your table saw.
Most manufactured extenders add 10-20 inches to a tabletop.
Readjust the Fence
Most modern table saws have an adjustable rip fence. In fact, saws that don’t have an adjustable rip fence are pretty rare nowadays.
To increase rip capacity on a saw that has an adjustable rip fence, simply extend the fence accordingly.
If you extend the rip fence as far as it can go and there’s still material hanging over the opposite end of the table, this may not be the end of the world, especially if the material is sturdier.
Also, if your rip fence extends outward but there isn’t much table underneath it when it does, such can lead to imprecise cutting.
In this instance, you should extend the fence to the end of the table and then add a tabletop extender at the opposite end.
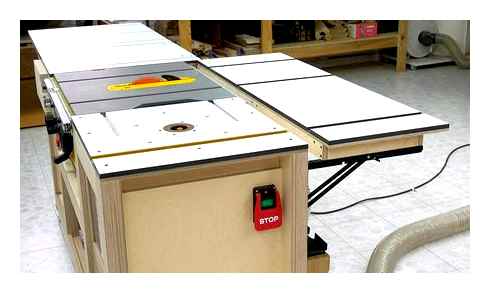
Here’s a video to learn more about extending the rip capacity for your saw.
Hi, I’m Emilee. I’m a woodworker, crafter and world class figure-outer. Mama Needs a Project is where I share all of my DIY adventures. I believe down to my core that working with your hands to physically create something will change your life!
I hope browsing Mama Needs a Project will leave you inspired and fired up to tackle your next DIY project. While Emilee is no longer actively blogging, her passion for woodworking can be found anywhere she goes.