Lawnmower fuel filter direction. Fuel filter information
Fuel filter information
There are (3) fuel filters in most paramotors: a pickup tube filter, an inline filter, and the inlet fuel filter screen which is inside all diaphragm carburetors. These three filters are replaceable. The inline filter is the most important of the three. If it is a cheap one or is missing, the inlet filter screen in the carburetor will likely clog and cause a lean condition (and overheating) or power fade/stall at or near full throttle.
A. Pickup tube filter (clunk)
Most clunks are the inexpensive variety like this one. It does not have a steel ball to weigh it down but relies on the weight of the metal frame of the clunk, instead. This clunk works on weed whackers but is not recommended for paramotors because of its low flow rate and how easy it tends to clog, especially if ethanol fuels are used.
Below is a typical OEM clunk. It contains a steel ball but it is only for adding weight to the clunk and does not provide any check valve function. A plastic clunk with some sort of metal weight might will tend to float in the gasoline.
Because most paramotors have priming systems, check valves in the clunk are largely unnecessary. However, if the pump check valves inside the carburetor are not working well enough to keep the fuel from running back through the fuel lines, there are other serious problems that must be fixed. Namely, the internal fuel pump will not be able to keep up with the fuel demand of the engine. The only fix for this is a carburetor rebuild. Pilots will eventually discover that when idle is erratic or difficult to adjust, it is time for a rebuild.
Generally, a clunk with a filter of fine, porous material (like those in the above photos) are only necessary if there is no inline fuel filter on the engine, which is rare. Unfortunately, these types of filters become clogged more easily with dirt including the goo from using ethanol fuels (when the fuel comes in contact with water). Cold weather can also choke fuel movement through this kind of filtering material due to the oil in the gasoline getting more viscous as the temperature drops. Before there was gasoline with ethanol, clunks served a more important purpose by helping keep water out of the fuel lines.
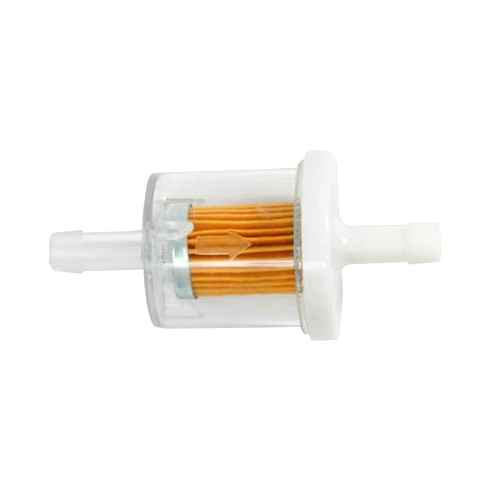
INCREASING FLOW THROUGH A CLUNK Pilots can modify clunks so that fuel will flow more easily through it. 1. Remove the filter from the tank. 2. Drill (2) 6mm (1/4) holes in the sides of the clunk. If there is a steel ball, do not remove it. If the holes are made too large, the ball may fall out.
Some OEM clunks have nipples with a narrow ID. This can restrict fuel movement, especially at or near full throttle. Use a 1/8 (3mm) drill bit to widen the ID of the nipple. Remember that ease of fuel flow through the entire fuel system is a critical requirement for good engine operation and preventing overheating/stall/fade.
CLUNK FLOW CHECK To determine if a clunk with a filter is in order is easy: Disconnect the fuel line at the inlet side of the inline fuel filter. Put a cup or container underneath the end of the disconnected fuel line so gasoline does not go everywhere. Pressurize the fuel tank with the primer tube or squeeze the primer bulb. Gasoline should pour out the end of the fuel line but not dribble. If there is any doubt, replace the clunk or make holes in it. If the clunk is like the one pictured below, it may be cleaned with compressed air.
QUALITY CLUNK This quality clunk has a 50 mesh stainless steel screen with a body made of brass. Cost: 8-10 on eBay. This clunk costs much more than the typical clunk shipped with paramotors, does not have to be modified, and is easy to clean. However, these clunks usually have a check ball which should be removed, an easy task done by forcing the butt end of a drill bit down the nipple. The bit will push the slight indentation in the brass fitting outwards and the small check valve ball will fall right out. I recommend drilling out the check valve seat inside the clunk to at least 1/8 (3mm).
CHEAP CLUNK AND CHEAP FUEL LINE Here is a photo of what typically happens to some clunks over time. The fuel line will split at the clunk and will separate from the fuel pickup tube and then bounce around inside the tank. Pilots should take a look in their fuel tanks periodically to be sure the clunk is not only attached but also does not have a split fuel line attached. If possible replace the OEM with a high quality clunk, like the one pictured above.
B. Inlet valve filter screen
The inlet valve filter screen in all diaphragm carburetors can only be cleaned or replaced if the carburetor is disassembled. It should always be checked if there are any fuel delivery problems in the engine i.e. fuel starvation. NEVER OPERATE AN ENGINE WITHOUT THIS SCREEN. Please see the carburetor rebuild page for photos and more info.
C. Inline fuel filter
(If desired, go to the filter installation steps directly and skip the discussion below)
Recommended inline fuel filters for paramotors which are available from various Internet sources.
- Miniplane OEM fuel filter
- Oregon 07-124
- WIX 33001 (the WIX has the highest capacity of any inline filter and can be used with the FSM)
Do NOT buy inline fuel filters sold in auto parts stores (other than the WIX 33001 which some stores stock). They are of inferior quality and will not block the small particles that clog the inlet valve filter screen and other small passages in the carburetor. Unfortunately, most inline filters are rated at 40 or more microns which is fine for 4 stroke engines but not enough for 2 stroke engines which have an inlet fuel filter screen that must be kept perfectly clear.
Why bother with a high quality filter? In two stroke engines, the fuel filter is also the engine oil filter. It must be able to trap all of the grit and other contaminants in the fuel and lubricating oil.
The engine that had this carburetor had trouble leaning out and stalled under load. Is it any wonder? Dirt in the fuel got inside the carburetor and clogged it. The arrow points to the small cavity on the outlet side of the fuel pump, just before it goes through the inlet needle valve filter screen. The pilot had an inline filter but it was one of the sintered bronze types (see below) commonly used on lawnmowers.
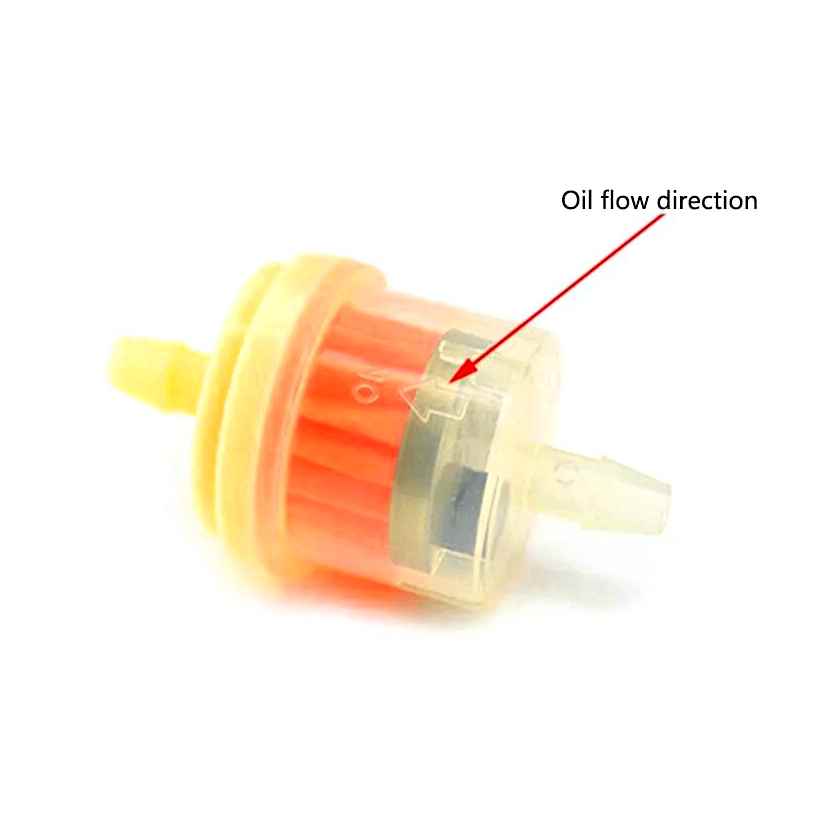
A CLOGGED FUEL SYSTEM IN ANY HIGH PERFORMANCE ENGINE IS A POTENTIAL DISASTER. FUEL STARVATION IS THE #1 CAUSE OF ENGINE DAMAGE IN PARAMOTORS.
Aviation engine forums (ROTAX) note that paper filters are the best because they have the finest filtration media – around 12 microns vs. 40 micros for sintered bronze or the pickup tube filters (clunks) sitting at the bottom of fuel tanks. The non-paper filters do not trap the small particles which will clog the pump inlet fuel filter screen in the carburetor. A clear filter housing must be used because pilots need to be able to periodically check that the filter is not clogged or damaged.
Here is a clogged inlet filter screen (diameter about 6mm) with a new one to the right. Sintered bronze filters will allow contaminants to reach the carburetor and why they should not be used. This engine experienced fuel starvation and overheated. Unbelievably, some paramotors do not even come with an inline fuel filter.
Here is another photo of a clogged inlet fuel filter screen. The pilot of this engine had trouble at full throttle – when fuel demand outstripped the supply. It is likely that this engine had no inline fuel filter or that it was the useless bronze sintered-type filter. I continued to be amazed at how simple maintenance will ensure our engines run well.
Below is a photo of a sintered bronze filter. The media is just not fine enough to stop small particles from passing through. These work satisfactorily in 4 cycle lawnmower engines, more or less, but in nothing else.
Fuel pump diaphragm showing signs of water contamination in the fuel, probably from using ethanol blends.
Below is a photo of the WIX 33001 inline fuel filter (L) and a similar filter (R) sold by the auto parts stores. The only problem with the WIX is that it is about twice the size of the OEM filters and may take a bit more thought as to where to put it. If you fly in very cold weather, this filter has better flow characteristics because of its large filtering area. The WIX filtering media is 12 microns which is excellent for all paramotors. Who knows what it is of the filter on the right. The fuel line nipples on the WIX have barbs which ensure that the connection will not leak. The filter on the right will tend to leak fuel because it has no barbs on the nipples. In addition, the fuel lines may come off if subjected to a pulling force. Does it make sense to put a cheap fuel filter on a 2,000 engine?
If the WIX filter is used on the Miniplane Top 80, its large size has to be considered. A possible location (shown here) is outside of the upper right engine mount, between it and the airbox. The downside is that the top of the fuel line tubing will be even further above the level of fuel in the tank. This will create a greater vacuum on the fuel and increase the chance of fuel vaporization at the most inconvenient times. Placing the WIX in the same location as the OEM filter or lower is a tight fit and it may rub on things. Keep an eye on it to sure the filter is not damaged.
This photo shows the WIX used in the FSM. Note how it is installed by the use of a short piece of 1/4 (6mm) automotive fuel line and a zip tie. This type of mounting parts on a paramotor is secure and reduces the effects of vibration.
The Oregon 07-124 is a commercial grade chainsaw filter rated at 10 microns. However, the filter has burrs (ridges) on the nipples from the injection moulding process. As we have discovered, it is source of small leaks, even when clamps are used. The leaks are not a hazard but pilots will notice the buildup of oil at the filter nipples over time. To fix this, remove the burrs with a razorblade. Why does Oregon not clean them up? It would involve another manufacturing step and increase the filter’s cost. Otherwise, these are excellent filters and superior to OEM’s from Italy because they have no metal parts which can corrode and rust. The Oregon’s low fuel flow rate is fine for OEM paramotors but not for those that have the FSM installed.
Depending on use, fuel filters should be replaced yearly at a minimum. As the filter is used, its flow rate declines from the presence of invisible particles. This is not much of an issue in automobiles but it is for paramotors because they sometimes run at full throttle for a relatively long time. Fuel starvation is a huge problem for paramotors and must be avoided to prevent overheating and the destruction of these air cooled engines.
Note: ethanol fuel blends and fuel that is contaminated by water hasten the deterioration of paper fuel filters.
Installation instructions
Here are some tips on fuel line installation, the various types, and where to purchase.
- If existing tubing is hard to remove, heat the tubing with a hot air gun or a hair dryer until it is almost too hot to touch. The tubing will easily slip right off of the fittings without damaging anything. If the heated air blown on the skin is painful, decrease the heat setting. It is possible to melt the fuel line so be careful.
- When connecting the new filter, heating the fuel line as above is helpful. Also, putting a small amount of 100% silicone grease on the fittings and inside the tubing eases the installation. It will also help keep it from splitting, a common problem with anything less than premium fuel line.
- Be certain to run fresh fuel through the system when replacing a fuel filter. Here’s how: Before connecting the fuel line from the filter to the carburetor, prime the system as if for starting. Put the end of the open fuel line in a container of some sort, and force fuel through the new filter into the container. At least a 1/2 cup (125 ml) should be enough. The fuel in the container can be put back in the fuel tank, if desired. If the step is not done, the inlet valve filter screen in the carburetor may become clogged.
- Complete the connection of the fuel line to the carburetor.
Honda Lawn Mower Fuel Shut Off Valve Position – With pics
A fuel valve is not fitted to all mowers but is fitted to all Honda mowers. The valve is also known as a gas valve, gas tap, fuel flow valve, petrol valve, gas shut off valve, gas shut off the tap – you get the idea.
So, where is the Honda lawn mower valve positioned? The Honda walk-behind mower fuel valve is fitted below the gas filler cap beside the black square air filter cover.
The nice people in Japan put a sticker on the engine cover to show the gas on and off position.
This post should have you covered, but if you need video help, check out “Turn gas on and off video.” The mower repair video library also includes other helpful Honda troubleshooting and maintenance videos.
How to Use it?
It’s a tap. You know what to do, turn counterclockwise for on and clockwise for off. When left unused, they can become stiff, though.
What’s it Do?
It allows the operator to block the flow of gas from the gas tank to the carburetor. All Honda mowers are fitted with one. Some are plastic and are fitted in the gas line. Others are built into the carburetor.
On some of the older Honda mowers, the fuel valve is built into the on/off control lever, so fuel is automatically shut off.
Where – The Honda Fuel Valve is found on the right side of the engine, as viewed from the front of the mower.
When to Use it?
The valve should be used when the mower isn’t in use. Ideally, after you’ve mowed the lawn, the gas should be shut off until the next use.
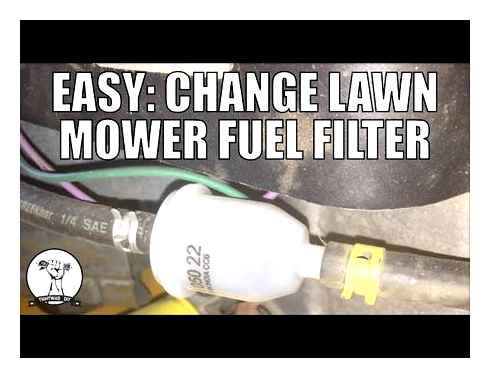
This takes the load off the carburetor float needle, prevents fuel evaporation and gas leaks. It’s also good practice to shut the gas off before transporting the mower in a car or trailer.
The constant bumping around would otherwise cause gas to flood the engine. This usually results in a no-start. Turn the gas off before making repairs, tune-ups, blade sharpening, cleaning, or anytime you need to turn your Honda mower over.
Turning Your Honda Over
Before you turn your Honda mower over, you first need to make it safe. To do this, turn the gas off and remove the plug wire. This will prevent the mower from starting, and you get to keep your fingers.
Honda mowers need to be turned over with the carburetor side up. That’s the side with the air filter. This prevents gas from spilling from the carburetor onto the air filter.
When gas spills onto the air filter, it prevents the engine from getting the right amount of air. This usually causes poor running and black smoke. This is a common complaint. The fix is simple, replace the filter, no harm done.
Gas On – Fuel valve in the on position.
Gas Off – Fuel valve in the off position.
Turn Over – Always carburetor side up.
Related Questions
Common Honda lawn mower problems? Honda mowers are very reliable. Some of the more common wear and tear complaints include:
How to drain gas from a Honda lawn mower?
Hey, I’m John, and I’m a Red Seal Qualified Service Technician with over twenty-five years experience.
I’ve worked on all types of mechanical equipment, from cars to grass machinery, and this site is where I share fluff-free hacks, tips, and insider know-how.
And the best part. it’s free!
Screen vs. Paper Fuel Filters for Small Engines
Paper fuel filters use filter elements made of polymer resin (phenolic resin) treated cellulose. This filter paper is considered a nonwoven filter media. Polyester felt sheets are another type of nonwoven filter media used for inline fuel filters.
Screen fuel filters use fine mesh screen filter elements. This screen is made of woven monofilament plastic or metal wires.
Fuel Filtration for Demanding Outdoor Power Equipment ApplicationsAll ICE (internal combustion engine), Outdoor Power Equipment (OPE), and Powersports machines require fuel filters to protect sensitive fuel system components. Optimized fuel filtration plays a significant role in maintaining consistent machine performance and improved longevity for more demanding applications.
Commercial groundskeeping, off-road Powersports and commercial-grade portable power generation are typical of these sorts of applications. Manufacturers build these machines with robust materials for handling rougher conditions. Notably, these machine designs include easy access for regular maintenance to maximize their service life.
Small engine applications
Applications where fuel system maintenance is critical for reliable engine performance:
- Portable power generation, primarily commercial grade generators
- ATV, UTV and utility vehicle maintenance and maintenance services
- Outdoor power equipment such as zero-turn, stand-on mowers, and snow blowers
- Off-road fleet, Powersports, and commercial small engine maintenance and fleet maintenance operations (MROs)
Why is fuel filtration for these small engine applications so demanding?
- Safety and durability requirements
- Performance requires higher, reliable fuel flow even at full load
- Designs provide easy access for carefully managed maintenance
- Machinery and repair costs that encourage maximizing its working life
Maintenance and repair management, fuel systems and fuel filter requirements:
- Filters durable enough to have a practical filter life
- Efficient filters that provide effective particle capture
- Filters that create no engine performance issues under full load
- 10% ethanol compatibility plus a broad resistance to alcohol exposure
Protecting modern ICE engines means using fuel filters resistant to alcohol exposure from different ethanol-gasoline blends, including E85. This alcohol resistance should include resistance to methanol exposure from fuel additives.
Protecting expensive machinery also means maximizing its life. Practical economics requires reliable fuel system component protection and fuel filters that are:
- Made to industry standards
- Made with high-quality materials
- Made using recognized good manufacturing practices (GMP)
Screen vs. Paper Filter Media
Screen filter elements
Small plastic inline gasoline filters typically use nonwoven filter components made of polymer-treated cellulose (paper) or synthetics like polyester felt.
Pleated paper and felt nonwoven filter elements have higher working surface areas and greater mechanical strength within the filter element. Maximizing filter element surface area increases flow through the filter while reducing flow restriction and pressure drop. A larger surface area also captures small particles more efficiently over time without reducing the filter’s flow rate much.
Screen vs Paper: Pros and Cons
Particle capture
Mesh captures particles on its surface, aka sieving
Paper and felt capture particles on the surface and within the filter media
Cleanability
- Surface capture filter elements can be flushed out of a filter using backflushing or backwashing
Paper and felt nonwoven filter media
- Nonwoven filter media cannot be usefully cleaned or refreshed
- Attempted cleaning by backflushing can damage nonwoven filter media
Size
Screen filters are physically smaller than paper or felt filters with comparable flow rates. This smaller size makes them useful where space requirements are critical.
What About Fuel Flow and Flow Rates?
Small internal combustion engines require higher flow rates to power commercial-grade machines. This higher performance requires adequate fuel flow rates provided by fuel pumps, not gravity feed.
- Lower flow rates than mesh filters
- Pleating and larger filter element sizes help to increase flow
Flow matters for maximum fuel pump life
Screen filters before fuel pumps offers protection without restricting flow. Restricted flow places stress on the pump, leading to a shorter working life.
Fuel system components susceptible to clogging and erosive wear need fine particle protection. Install fuel filters with nonwoven filter elements (paper or felt) downstream of the fuel pump but just upstream of the engine. The fuel pump can then push enough fuel through the finer filter to avoid fuel starvation.
Estimating fuel flow for small engines
Small engine manufacturer specifications may provide fuel consumption rates. Base fuel consumption estimates on engines running at full throttle and under load. Use these estimates for determining filter flow requirements.
Matching fuel flow to maximum demand ensures enough fuel is provided to the engine, preventing fuel starvation. Full throttle under load is when good engine performance is most important. If fuel consumption rates are unavailable, estimate small engine fuel consumption at between 0.4 and 0.6 pounds per hour per horsepower.
Horsepower x Fuel Consumption = Pounds of Fuel Per Hour
The following fuel weights per gallon are approximate because the weight of gasoline can vary slightly between brands and grades:
- Diesel 6.9 pounds per gallon
- E85 gasoline 6.6 pounds per gallon
- Gasoline (E0, E10 and E15) 6.2 pounds per gallon
The engine’s fuel flow requirement is the pounds per hour divided by the weight of the fuel per gallon.
Pounds of Fuel Per Hour / Pounds Per Gallon = Fuel Flow Requirement
What is ANSI/OPEI, and Why Does It Matter?
What advantages do ANSI-compliant filters have over non-compliant filters? Certified testing to Outdoor Power Equipment performance requirements ensures parts have the quality and durability needed for real-world conditions.
ANSI/OPEI B71.10 certified, independent testing standards
- Durability, sturdiness, and safety
- Material compatibility with both gasoline and 10% (E10) ethanol-blended gasoline
No ethanol, according to the OPEI, is ideal for outdoor power equipment. However, pure non-ethanol gas (E0) is becoming increasingly expensive and challenging to get. It is reasonable to assume that Powersports and Outdoor Power Equipment will be exposed to E10 or other ethanol-gasoline blends.
How ITW OEM small engine filters go beyond ANSI performance standards
ITW fuel filters provide superior compatibility with E-85 ethanol-gasoline and good resistance to methanol exposure from fuel additives.
Superior design
Superior materials
PETg filter bodies instead of just PET
- robust, more impact and heat resistant
- Higher chemical resistance, especially to alcohols
Impact and heat modified engineering grade nylon instead of commodity nylon filter bodies
- robust, more impact and heat resistant
- Higher chemical resistance, especially to alcohols
304 stainless steel instead of brass or lower-grade steels
The Best Small Engine Fuel Filter Option?
Installing a screen filter upstream of the fuel pump with a nonwoven paper or felt filter downstream provides optimum fuel system protection and performance.
Large micron ratings capture coarse particles
Protect fuel pumps from damage by capturing coarse particles. Because mesh filters are high-flow filters, they should be installed upstream of a fuel pump. In general, use mesh screen filters with micron ratings between 75 and 150 microns for pre-pump filters.
Small micron ratings capture fine particles
Fuel filters with low micron ratings capture smaller particles. They protect sensitive fuel system component damage caused by fine particle erosion and clogging. These finer filters generally use nonwoven filter elements like polyester felt sheets and polymer resin-treated cellulose (paper).
Filter elements made of these types of materials are usually pleated. Also, the filters themselves tend to be physically larger than mesh screen fuel filters. The larger size and pleating increase the filter’s effective surface area, which maximizes flow.
Filters with nonwoven filter components have micron ratings ranging from 10 microns or lower to as high as 80 microns. Install these filters downstream of fuel pumps and near the engine to protect fuel system components from fine particle damage.
Conclusion
Fuel pumps are necessary for demanding small engine applications with higher fuel flow rates. Install fuel filters with paper or felt filter elements downstream of fuel pumps and close to the engine.
Place screen filters with about 100-micron ratings and adequate flow rates just upstream of the pump. Manufacturer recommendations for placement and filter micron ratings should always override these rules-of-thumb. Also, use fuel filters with high enough flow rates that engines always perform well under full load. It is necessary whether the machine uses a gravity-fed flow or a fuel pump.
Use fuel filters and valves tested to and compliant with ANSI/OPEI B71.10 performance testing standards.
Related blog posts
- Plastic Fuel Filter Body Materials The choice of body plastic is vital for small inline fuel filters. They must be sturdy, durable, and reliable in Powersports and Outdoor Power Equipment. The best body material plus sound engineering makes all the difference in quality OEM fuel filters.
- ANSI/OPEI B71.10 Compliant Fuel Valves and Filters The ANSI/OPEI B71.10-2018 standard went into effect 12-Nov-2020. Learn more about ANSI-compliant plastic fuel filters and fuel shut-off valves. Find out how independent, third-party testing in certified labs confirms material and manufacturing quality by exposing critical fuel system components to stresses that mimic real-world operating conditions.
- Sintered Porous Bronze Fuel Filters, Part 1. What They Are and Their Use in Small Plastic Inline Fuel Filters Why bronze filter elements for plastic inline fuel filters? Find out more about sintered porous bronze filter elements and their use in small plastic inline fuel filters. ANSI/OPEI B71.10-2018 compliant ITW Visu-Filters Filters for light-duty carbureted vehicles, Outdoor Power Equipment and Powersports use them.
Take Advantage of Our Expertise
We offer a line of ideas, so if you don’t see it. ask for it. Let us turn your ideas for pneumatic or fluidic circuitry assemblies into reality — from conception to finished product.
Categories
- Subscribe to our blog
- About ISM
- Cause Marketing
- Check Valves
- Custom Services
- Customer Services
- Customer Success
- Employee Spotlight
- Hose Barb Connectors
- How To
- Inline Filters
- Materials
- Miniature Valves
- Miscellaneous
- Packaging
- Precision Orifices
- Product Spotlights
Solved! Husqvarna Lawn Mower Isn’t Getting Fuel
Your Husqvarna mower doesn’t start or it’s running sluggishly. You have narrowed down your problem to the fuel system, but now you’re not sure just where to start. I have put together a list of items to check on your mower along with steps to troubleshoot and repair your fuel supply problem.
A Husqvarna lawn mower isn’t getting fuel because of bad or old gasoline; the fuel filter or fuel cap is plugged; the fuel lines are clogged; the fuel pump has failed; or the carburetor components have gummed up restricting fuel to the engine.
This post may include affiliate links. Purchases made through these links may provide a commission for us, at no extra cost to you. As an Amazon Associate, we earn from qualifying purchases.
Follow all safety instructions provided in your equipment operator’s manual before diagnosing, repairing, or operating. Consult a professional if you don’t have the skills, or knowledge or are not in the condition to perform the repair safely.
Reasons Your Husqvarna Mower Isn’t Getting Fuel
Bad or Old Gasoline in Your Husqvarna Lawn Mower
Gas that has been sitting in your Husqvarna mower for long periods of time can break down. The ethanol in your fuel attracts moisture.
This combination of ethanol and moisture can cause gummy deposits in your fuel system that can cause restrictions. When these components become clogged, your mower will no longer get fuel.
Use unleaded gasoline with a minimum octane rating of 87 and a maximum ethanol content of 10 percent. Because fuel can begin breaking down as quickly as 30 days after purchase, it is important you use your gasoline within a short period of time.
If you are unable to do so, use a fuel additive to stabilize your fuel. I like to use an additive in every tank of fuel so I can minimize the problems that can develop from running old fuel in my mower.
I prefer to use Sea Foam Motor Treatment as an additive. It is a petroleum-based product that not only stabilizes fuel, it also cleans the fuel system. Read more about the advantages of Sea Foam and the best fuel to use in your Husqvarna in these articles.
Repair: Remove old fuel using a fuel siphon and place it in an approved fuel container to recycle at a later time. Refill your fuel tank with fresh fuel with an additive to stabilize and clean your fuel system.
Husqvarna Fuel Filter is Plugged
Your fuel filter prevents dirt from entering the fuel system and contaminating the engine. The dirt that collects in the filter can plug it preventing fuel flow.
It is good practice to change your fuel filter annually during the full maintenance of your Husqvarna mower. This should prevent you from running into clogging filter problems during the mowing season.

Repair: Replace your fuel filter with a new filter. When installing, make sure the arrow on the side of the new fuel filter is pointed in the direction of the fuel flow. The arrow should be pointed away from your fuel tank and toward the carburetor.
Clogged Fuel Lines on Your Husqvarna Mower
The fuel lines on a Husqvarna mower can become clogged due to running old fuel. A gummy residue can be left behind preventing fuel to flow to the engine. To find a clog in your fuel lines, use your fuel shut-off valve to start and stop fuel. You can also crimp the line to stop the flow.
Check to make sure you have fuel flow running through your fuel lines. Do this by shutting off your fuel flow and removing the end of a section of the fuel line furthest from the fuel tank. Place this end in a container and start your fuel flow.
Make sure the container is placed lower than the fuel tank because fuel cannot run uphill without the help of a pump. If you don’t have fuel running into the container, your fuel line is plugged. Follow the repair instructions to remove the clog.
Repair: To remove the clog in your fuel line, shut off your fuel supply and remove the section of the line that is clogged. Spray carburetor cleaner into the line. This is used to help loosen the clog. Follow with blowing compressed air into the line to remove the clog.
If you are unable to remove the clog in the line or you notice your fuel line is dry and cracked, you need to replace it with a new fuel line.
Bad Fuel Pump on Your Husqvarna Mower
Over time your fuel pump can fail. Fuel sitting in your fuel pump can degrade the component or it can wear from normal use.
When it fails, the pump is no longer able to create the pressure it needs to push fuel up to the carburetor. Your Husqvarna’s engine will not get the fuel required to start and run.
Before you begin testing your fuel pump, confirm you are getting fuel to the inlet port on the pump. You may have already confirmed this by checking fuel flow through your fuel lines.
If not, check to make sure fuel is able to flow through the line attached to your fuel pump’s inlet port before checking your fuel pump.
Repair: Replace a fuel pump that is unable to pump fuel to the carburetor. Do this by removing the fuel line from the carburetor and placing it in a container.
Start your engine and watch for a steady or pulsating flow of fuel from your fuel pump. If you don’t see this constant flow, your fuel pump is bad.
Dirty Carburetor on Your Husqvarna Mower
The Husqvarna mower’s carburetor is essential to making sure the engine receives the correct mixture of fuel and air. When the carburetor is dirty and clogged, it may restrict fuel from getting to your engine.
Fuel can leave gummy substances and crusty deposits preventing your carburetor from functioning properly.
Before you start tearing apart your carburetor to find the clog and clean it, take this quick step to determine whether the carburetor is a problem.
Remove the air filter from the housing and spray carburetor cleaner into the air intake. Start your engine. If it starts and runs for a bit and then shuts down, you need to clean your carburetor.
Repair: I recommend tackling the job of cleaning the carburetor yourself if you are a little mechanical and don’t mind working with small parts. If that’s you, follow my step-by-step directions in this guide to clean your carburetor.
If you are not this person and choose not to clean your carburetor, you can either replace it or have your local lawn mower repair shop clean it for you.
If you choose to replace it, have your engine model and spec number to ensure you receive the right part. This is not to be confused with the mower model and serial number.
Most lawn mower manufacturers utilize other manufacturers’ engines such as Briggs and Stratton, Kawasaki, Honda, and Kohler to name a few major players in the small engine market. You can usually find the model and spec on the engine cover.
I have found some manufacturers may only use a QR code that you will have to scan to get this information. You can easily scan it with a QR reader using your cell phone to obtain the details.
Clogged Husqvarna Mower Fuel Cap
Your Husqvarna fuel cap is designed with a vent to allow air to pass through the cap. When the vent is plugged restricting airflow, the fuel tank will act like a vacuum and prevent fuel from flowing out of the tank.
Repair: Run your Husqvarna mower for a while with and without the fuel cap in place. If the mower continues to run fine without the cap but shuts off after a while with the cap in place, chances are your fuel cap is plugged.
You can attempt to clean it to remove the clog. If this doesn’t work, buy a new Husqvarna fuel cap.
Keep Your Husqvarna Fuel System Clean
Use the correct kind of gasoline for your gas-powered lawn mower. Choose a gas with a minimum octane rating of 87 and a maximum ethanol content of 10%.
The lower the ethanol content the better. Refrain from using E15 and E85 fuels that are popping up at more fuel stations today. These fuels contain 15% ethanol and 85% ethanol respectively.
Make sure the fuel is fresh and being used timely. Add a fuel additive to stabilize and clean your fuel system, like Sea Foam Motor Treatment, so you don’t have to worry about consuming the fuel within a certain timeframe. Sea Foam can stabilize your fuel for up to two years.
Husqvarna Mower Still Will Not Start
If you are still having a problem with your Husqvarna lawn mower not wanting to start after checking out the items above, you may have a different starting issue.
Read my article on reasons a Husqvarna mower will not start to identify other causes of starting problems.
Still Having Problems with Your Husqvarna Lawn Mower?
If you are still having problems with your mower, check out my guide on common problems owners encounter with their lawn mowers.
I put together a chart to identify causes and solutions to problems including starting, smoking, cutting, vibrating, dying, and more.
If you don’t feel comfortable troubleshooting and performing repairs on your lawn mower, it’s best to contact your local Husqvarna dealership or lawn mower repair shop for assistance.
You must remain safe and only perform repairs you are mechanically able to perform to avoid injury or further damage to the mower.
Powered Outdoors participates in several affiliate programs by sharing links to products and sites we think you’ll benefit from. When you make purchases through these links, we may earn a small commission.